How Does Robotics Aid Occlusion Testing For Drug Delivery Devices?
By Stephen Prabu
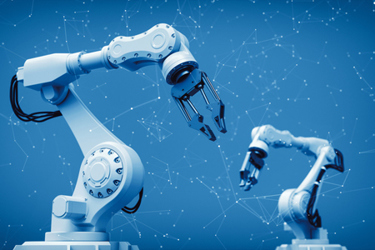
Occlusion testing using robotic automation for medical devices, such as infusion pumps, catheters, IV lines, insulin pumps, ventilators, and other drug delivery systems, involves robotic systems to simulate, detect, and resolve occlusions under controlled, repeatable conditions. Robotic automation testing helps the engineers confirm the fix during reliability testing and improves the accuracy of identifying the occlusion.
Why Occlusion Testing Is Critical
Occlusion testing is critical for confirming the safety and efficacy of medical devices, particularly infusion pumps, catheters, and other drug delivery systems. Interrupted or reduced medication flow produces occlusion, leading to under-dosing, delayed treatment, or even overdosing if not correctly detected and addressed. In recent years, FDA recalls have occurred more due to the safety and reliability of infusion systems used in medical treatments, primarily due to occlusion issues. In 2022, over 19 million infusion systems from Smiths Medical were recalled following reports of tubing occlusions that contributed to 1,571 incidents, including 14 injuries and two fatalities.1 Similarly, in 2021, 250,000 infusion pumps were recalled due to a failure to re-alarm in cases of repeated upstream occlusions.2 If an upstream occlusion alarm was triggered but not fully resolved, the pump sometimes failed to re-alarm, posing risks during the administration of critical fluids. In 2023, Braun recalled 10,600 devices due to occlusion issues, leading to 51 complaints, one injury, and one death,3 highlighting the continued safety challenges surrounding infusion systems. The problem continued into 2024, and InfuTronix, LLC recalled 50,000 Nimbus infusion pump systems due to occlusion-related risks, among other issues.4
Benefits Of Robotic Automation For Occlusion Testing
- Robotic systems can precisely reproduce the exact occlusion scenarios in multiple devices and eliminate the variability that might come with manual testing.
- Automation allows for the simulation of a wide range of occlusion conditions, including partial blockages, complete blockages, patient movement, or changes in tubing.
- Real-time sensors in robotic testing systems detect occlusions 40% faster than manual methods, allowing quicker response and resolution of blockages.5
- Robotic automation minimizes the need for human intervention and reduces potential errors. It enabled round-the-clock trial testing, improving overall test coverage by 50% for Medtronic.6
- Automated testing helps manufacturers meet rigorous safety standards, including FDA and MDR guidelines.
Critical Components Of Robotic Automation
- Robotic Arm for Precise Control: The arm manipulates the infusion system's tubing, catheters, or delivery lines to simulate different occlusion scenarios. It includes creating intentional kinks, twists, or compressions in the tubing to test how the system responds to reduced or blocked flow. Robotic arms improved occlusion detection accuracy by 30% compared to manual testing due to the robot's ability to apply precise pressure and consistently manipulate tubing at controlled angles.7
- Automated Fluid Handling Systems: Robotic systems can automatically simulate real-time infusion conditions by varying flow rates, pressure, and fluid types. They allow for precise and repeatable device testing under conditions that typically lead to occlusions. In tests with infusion devices, robotic fluid handling systems replicated real-time occlusion events and reduced test variability.8
- Sensor Integration for Real-Time Monitoring: Robotic occlusion testing systems are often integrated with pressure sensors, flow meters, and other monitoring tools that track real-time data during testing. Sensors are placed to measure how the infusion system responds to simulated blockages, pressure changes, or flow reductions. A report found that systems equipped with real-time monitoring sensors reduced occlusion-related malfunctions.9 The sensors continuously monitor pressure and flow rate changes, enabling faster and more reliable detection.
- Programmable Testing Scenarios: Robotic systems can be set to test various occlusion scenarios, including different degrees of flow rate accuracy with restrictions, tubing kinks, patient movements, or line blockages. Automation allows for consistent testing across multiple devices and confirms that each product undergoes the same rigorous validation process. It provides detailed feedback for improving device design and performance. Robotic systems are programmed to run over hundreds of distinct occlusion scenarios per device at the same time continuously to confirm that the infusion pump can handle various clinical situations efficiently. As per my observation, this level of automation accelerates testing cycles by 50% compared to manual methods.
- Closed-Loop Feedback for Dynamic Response Testing: Robotic occlusion testing systems can include closed-loop feedback, where the system detects the occlusion, automatically adjusts the infusion system’s flow, pressure, or operation in real-time, and tests how the system resolves the occlusion. Closed-loop robotic systems improved occlusion resolution success rates by 35% in testing,10 where the system autonomously adjusted flow and pressure to resolve the occlusion without manual intervention.
Process Of Robotic Occlusion Testing
- Setup of Device and Testing Environment: The medical device (e.g., infusion pump or catheter system) is connected to a testing rig with sensors, robotic arms, and fluid handling systems. Setup times for robotic occlusion testing were reduced by 20% due to the standardized configurations of rigs, which allowed for more efficient test case execution across multiple devices.11
- Simulating Occlusion Scenarios: The robotic arm can bend, twist, or compress the infusion line to simulate partial or total occlusions. Alternatively, the fluid handling system can simulate occlusions by altering the fluid’s properties (e.g., introducing thicker fluids that mimic blood clots) or changing the flow rate to simulate restricted or blocked flow.
- Real-Time Data Collection and Analysis: While sensors continuously monitor flow rates, pressure, and fluid dynamics during testing, the system records the time the infusion pump or catheter takes to trigger alarms, adjust flow rates, or correct the issue.
- Automated Occlusion Resolution: During reliability testing, the robotic testing system is connected with a self-correcting mechanism in the infusion pump. If the smart pump detects an occlusion, it will automatically reverse the flow, adjust pressure, or trigger a flush to clear the blockage. Self-correcting infusion pumps resolve occlusions autonomously in 92% of test cases, with robotic systems monitoring their effectiveness.12 They reduced the need for manual interventions and improved patient safety.
- Reporting and Data Logging: Reports are generated and uploaded to the cloud-managed system to provide detailed feedback on the device's performance under test. Robotic systems increase reporting accuracy by 25% compared to manual systems.13–15
- Repeatability and Stress Testing: Robotic systems can simulate long-term stress conditions to see how devices perform over extended periods, testing the durability and reliability of components in maintaining proper flow and detecting occlusions.
Robotic systems can detect and resolve occlusions in medical devices like infusion pumps, catheters, and insulin pumps by simulating real-world scenarios under controlled conditions. The integrated test setup of real-time monitoring, programmable testing, and closed-loop feedback mechanisms reduces testing cycles, decreases manual interventions, and improves the overall reliability of medical devices. Robotic automation in occlusion testing is the most required advantage in advancing lifesaving medical technologies' safety, performance, and innovation as the healthcare industry evolves.
References
- https://www.fda.gov/medical-devices/medical-device-recalls/smiths-medical-recalls-certain-cadd-system-administration-sets-and-cassette-reservoirs-issues
- https://www.fda.gov/medical-devices/medical-device-recalls/baxter-recalls-sigma-spectrum-infusion-pumps-master-drug-library-version-8-and-spectrum-iq-infusion#:~:text=Medical%20Device%20Recalls-,Baxter%20recalls%20SIGMA%20Spectrum%20Infusion%20Pumps%20wi
- https://www.fda.gov/medical-devices/medical-device-recalls/b-braun-medical-inc-recalls-infusomat-space-large-volume-pump-wireless-and-infusomat-space-large#:~:text=Reason%20for%20Recall,death%20related%20to%20this%20recall
- https://www.fda.gov/medical-devices/medical-device-recalls/infutronix-llc-recalls-nimbus-and-nimbus-ii-infusion-pump-systems-multiple-device-failures-may-cause
- https://qentelli.com/thought-leadership/insights/robotic-process-automation-vs-traditional-test-automation
- https://news.medtronic.com/2021-06-02-Real-World-Data-on-Over-4,000-Patients-Using-the-Medtronic-MiniMed-TM-780G-System-Demonstrate-Time-in-Range-Mirroring-Pivotal-Trial
- https://www.universal-robots.com/blog/automated-testing-improves-precision-and-repeatability-for-medical-device-quality-control/
- https://www.essert.com/life-science/medical-device-testing/
- https://www.smdsensors.com/resources/occlusion-sensing-in-medical-devices-an-in-depth-overview/
- https://blog.johner-institute.com/regulatory-affairs/closed-loop-systems/
- https://www.universal-robots.com/industries/medical-and-cosmetics/
- https://pmc.ncbi.nlm.nih.gov/articles/PMC7750013/
- https://pmc.ncbi.nlm.nih.gov/articles/PMC3644815/
- https://automata.tech/blog/the-benefits-of-lab-automation-for-diagnostic-testing/
- https://www.rapidinnovation.io/post/generative-ai-automated-financial-reporting-applications-use-cases-benefits
About The Author:
Stephen Prabu is a PMP certified senior technical program manager who has worked in client locations worldwide: Japan, Denmark, Germany, U.S., and India. He has 20 years of experience in managing large-scale teams involving technology migrations, software development, and process improvements. He is pursuing an MBA from Jack Welch Management Institute (U.S.) and holds a bachelor’s degree in engineering from Government Engineering College in India. He can be contacted via email at stevenprabu@gmail.com.