INJECTABLE DRUG DELIVERY ARTICLES
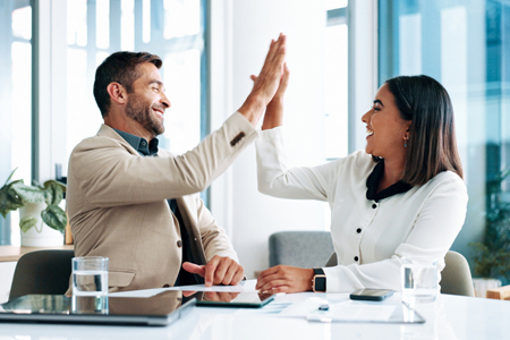
Early recognition and mitigation of drug and device integration difficulties are critical to the success of combination products. The collaborative effort in development cannot be overstated.
INJECTABLE DRUG DELIVERY RESOURCES
-
Jeff Clement, Executive Director, CDMO Business Development North America, discusses the impact of the pandemic on CDMOs and parenteral market trends.
-
The choice between closed and open fill/finish for cell therapy drug products ultimately involves a careful balance between safety, accessibility, efficacy, and the type of cell type used.
-
Examine the dynamic regulatory environment of drug-device combination products as well as concrete steps to take to navigate regulatory complexities and decrease time to market.
-
Explore the key findings of a new wearable injector clinical trial, including its positive impact on patient experience and the broader benefits of wearable injectors for chronic disease management.
-
Growing demand for high-value, complex therapies requires the right containment and delivery systems: solutions that offer superior quality and patient comfort while meeting stringent regulatory requirements.
-
Long-acting, complex drug delivery products, particularly those based on injectable microparticles, nanoparticles, and implants, are among the most attractive parenteral products.
-
The revisions to EU Annex 1 set the stage for the future direction of the pharma/biotech industry. Explore some of the key takeaways and interesting changes for risk management and contamination control strategies.
INJECTABLE DRUG DELIVERY SOLUTIONS
-
Subcutaneous
Low - Medium Viscosities
< 100 cP
1 - 10 mlHigh - Ultra-High Viscosities
>100 - 10,000 cP
0.5 - 3 mlArQ® - Bios offers a small, simple to use package to deliver high viscosity formulations. Oval’s proprietary COC PDC technology allows us to build the device around a stronger drug container that can deliver 1ml of formulations up to 1000cP through a 25G needle in less than 5 seconds. The ArQ-Bios platform also can deliver greater volumes than 1 ml subject to matching the formulation characteristics with acceptable patient tolerability.
-
Formulation and aseptic filling solutions are crucial at every stage of development. Consider a manufacturing partner who can address every challenge on the path from pre-clinical programs to commercialization.
-
By partnering with Battelle, your organization can reduce risks and save on investment costs, leading to more successful and sustainable outcomes.
-
Learn how our team of scientists, engineers, and human-centered designers, as well as our world-class facilities, empower us to confidently guide your product toward a successful market launch.
-
Syngene's Sterile Fill-Finish facility is custom-built to meet market demand for clinical supplies, sterile drug products having short development timelines,
-
With world-class facilities, the state-of-the-art equipment and some of the industry’s most talented people, you can feel confident that your small molecule drug product is in safe hands. Learning from decades working with other small molecules, INCOG has been purpose-built to provide better solutions for the global injectable drug product sector.
-
Our system is ideally suited for the production of pre-clinical, clinical and niche commercial injectable products in vial, syringe, and cartridge formats.
-
AST aseptic filling products address the unique processing requirements of biologics manufacturing to gently care for biologic products during the fill-finish process. Their highly accurate peristaltic dosing system uses single-use pharmaceutical grade tubing that has been optimized to keep shear stress to an absolute minimum. When exiting the fluid path through the filling needle, the motion control system maintains the fill needle within the container and slowly rises as the product is being dispensed to minimize splashing and foaming that could introduce stress to the product. Temperature controlled filling is also possible with the ASEPTiCell® and GENiSYS® systems. AST has experience dosing products at temperatures as low as 3°C.
-
Ascendia’s team of scientists have decades of combined experience in sterile supplies for clinical trials, making them expert at solving the most difficult formulation challenges. In short, we consistently make the insoluble soluble.
-
BD Physioject™ Disposable Autoinjector offers a proven, user-friendly platform for self-injection, enhancing patient comfort, safety, and adherence across multiple chronic disease treatments globally.